7 Common Challenges in High Volume Injection Molding and Solutions
- nubs plasticsinc
- Jun 28, 2024
- 2 min read
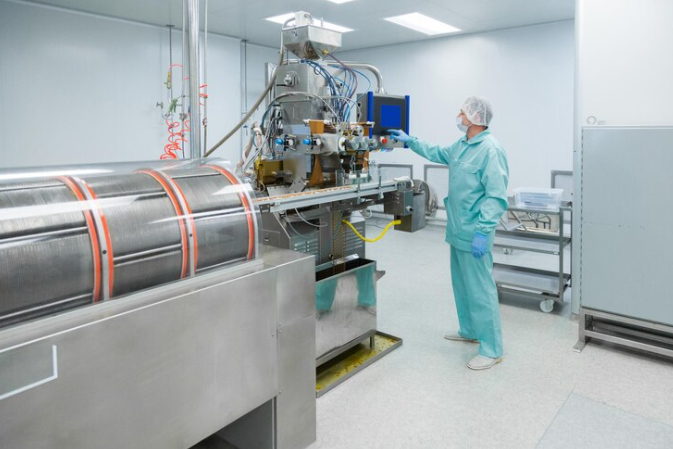
Explore the High volume injection molding plays a pivotal role in the plastic manufacturing industry, enabling the efficient production of large quantities of parts. However, with its advantages come several challenges that manufacturers often encounter. Addressing these challenges effectively is crucial for optimizing production efficiency and maintaining product quality. Here are seven common challenges in high volume injection molding along with practical solutions:
Tooling costs constitute a significant portion of the initial investment in high volume injection molding. Ensuring the molds are robust enough to withstand continuous use without frequent maintenance is essential. Solutions involve using high-quality materials for molds and implementing regular maintenance schedules to prevent downtime.
Minimizing cycle times is crucial to achieving high production throughput. Challenges arise from the complexity of parts and the need for cooling and ejection processes. Solutions include using advanced mold designs, optimizing injection parameters, and employing efficient cooling techniques like conformal cooling.
Maintaining consistent part quality across high volumes can be challenging due to variations in material properties, mold wear, and environmental factors. Solutions involve rigorous quality control measures, real-time monitoring systems, and automated inspection technologies to detect defects early.
Selecting the right materials that meet performance requirements while ensuring compatibility with the molding process is critical. Challenges include material shrinkage, warping, and degradation during repeated heating cycles. Solutions include conducting comprehensive material testing, optimizing processing conditions, and using additives to improve material properties.
Coordinating logistics for high volume production involves managing raw material supply, scheduling production runs, and optimizing inventory management. Challenges include ensuring timely delivery of raw materials and coordinating production schedules to meet demand fluctuations. Solutions involve establishing robust supply chain partnerships, implementing just-in-time inventory systems, and utilizing predictive analytics for demand forecasting.
Addressing environmental concerns such as plastic waste and energy consumption is crucial in high volume injection molding. Challenges include minimizing material waste, optimizing energy-efficient production processes, and adopting sustainable materials. Solutions include implementing recycling programs, using biodegradable materials, and investing in energy-efficient equipment.
Meeting regulatory requirements, particularly in international markets, presents challenges related to material safety, product labeling, and environmental regulations. Solutions involve staying updated on regulatory changes, conducting thorough compliance audits, and partnering with regulatory experts to ensure adherence.
In conclusion
while Plastic Manufacturing Company offers substantial benefits in terms of production efficiency and scalability, addressing these seven common challenges is essential for maximizing operational success. By implementing effective solutions tailored to each challenge, manufacturers can optimize their processes, enhance product quality, and maintain competitive advantage in the dynamic landscape of plastic manufacturing.
3.5
Comments